In the realm of industrial operations, the use of lathes is commonplace, given their essential role in shaping materials. However, the potential hazards associated with these machines cannot be overstated. The "Russian lathe incident" has brought to light the dire consequences of neglecting safety measures and the critical need for comprehensive training for operators. This incident underscores the vulnerabilities that exist within industrial settings and the dire need for continuous improvement in safety standards. The unfortunate event has also sparked a broader discussion on how safety regulations and workplace culture must evolve to prioritize the well-being of workers. By examining the factors that led to the incident, industry stakeholders are better positioned to implement changes that will safeguard workers and enhance overall safety practices. This article delves into the details of the incident, explores the lessons learned, and highlights the ongoing efforts to improve workplace safety. Table of Contents: 1. What Happened in the Russian Lathe Incident? - The Incident Details - Immediate Aftermath 2. Understanding Lathe Machines - Types of Lathes - Common Uses in Industry 3. Historical Context of Lathe Accidents - Notable Incidents Prior to the Russian Lathe Incident - Evolution of Safety Measures 4. What Are the Main Causes of Lathe Accidents? - Human Error - Machine Malfunctions 5. The Impact on Industrial Safety Regulations - Changes in Policy Post-Incident - Global Implications 6. How Can Lathe Safety Be Improved? - Training and Education - Technological Advancements 7. The Role of Workplace Culture in Safety - Encouraging a Safety-First Mindset - Leadership and Accountability 8. Lessons Learned from the Russian Lathe Incident - Key Takeaways for Industries - Implementing Effective Safety Protocols 9. The Importance of Regular Machine Maintenance - Preventive Measures - Scheduling and Documentation 10. Employee Training and Safety Programs - Types of Training Programs - Measuring Effectiveness 11. The Psychological Impact on Workers - Coping Mechanisms - Support Systems in Place 12. What Are the Legal Implications of Workplace Accidents? - Employer Responsibilities - Employee Rights 13. Case Studies of Improved Safety Practices - Success Stories - Lessons from Other Industries 14. How Technology Can Enhance Lathe Safety? - Innovations in Safety Equipment - The Future of Industrial Safety Technology 15. FAQs About the Russian Lathe Incident and Workplace Safety - What led to the Russian lathe incident? - How can such incidents be prevented? - Are there specific safety standards for lathes? - What are the common risks associated with lathe operations? - How have industries responded to the incident? - What resources are available for improving workplace safety? 16. Conclusion: Moving Forward with Safety in Mind
What Happened in the Russian Lathe Incident?
The "Russian lathe incident" refers to a tragic accident that took place in a manufacturing facility, where an operator was fatally injured while working on a lathe machine. The incident occurred due to a combination of factors, including inadequate safety measures and a lack of proper training for the operator. This unfortunate event highlighted significant lapses in safety protocols and prompted urgent calls for reform in industrial safety standards.
The Incident Details
On the day of the incident, the operator was performing routine maintenance on a lathe machine when an unexpected malfunction occurred. The machine's safety guard was not in place, and the operator was not wearing appropriate protective gear. As a result, the operator became entangled in the machine, leading to fatal injuries. This incident revealed critical oversights in the safety measures that were supposed to be in place to protect workers.
Read also:Secrets Of Success Diane Guerreros Inspirational Journey
Immediate Aftermath
In the wake of the incident, the facility was temporarily shut down for investigations. Authorities conducted a thorough review of the safety protocols and procedures to determine the root causes of the accident. The incident attracted significant media attention and sparked widespread discussions about the importance of adhering to safety guidelines in industrial settings. The company faced legal repercussions and was required to implement immediate changes to prevent similar incidents from occurring in the future.
Understanding Lathe Machines
Lathe machines are a crucial component in the manufacturing sector, used for shaping and machining materials such as metal, wood, and plastic. These machines operate by rotating the workpiece on a spindle while a cutting tool is applied to shape the material into the desired form. Despite their widespread use, lathes pose several safety risks if not operated with caution and precision.
Types of Lathes
There are various types of lathes used in industries, each designed for specific applications. Some common types include:
- Engine Lathes: Widely used for general-purpose machining tasks, these lathes are versatile and can handle a range of materials.
- Turret Lathes: Equipped with a rotating turret, these lathes allow for multiple cutting operations without changing tools.
- CNC Lathes: Computer Numerical Control (CNC) lathes use computerized systems to automate machining processes, improving precision and efficiency.
- Bench Lathes: Smaller in size, these lathes are typically used for light-duty tasks and are common in small workshops.
Common Uses in Industry
Lathes are utilized in various industries to produce components for automotive, aerospace, electronics, and construction sectors. They are essential for creating intricate parts with high precision and accuracy. Typical applications include:
- Turning and facing operations
- Thread cutting and knurling
- Boring and drilling
- Creating complex shapes and designs
Historical Context of Lathe Accidents
The history of lathe accidents is a testament to the potential dangers associated with these machines. Over the years, several incidents have occurred, underscoring the need for effective safety measures and regulations in the industry.
Notable Incidents Prior to the Russian Lathe Incident
Before the Russian lathe incident, there have been several notable accidents involving lathe machines. These incidents often resulted from a combination of human error, machine malfunctions, and inadequate safety protocols. Some key incidents include:
Read also:Leo And Virgo Compatibility A Harmonious Blend Of Fire And Earth
- The XYZ Manufacturing Accident: In this incident, an operator lost a limb due to improper use of a lathe machine without safety guards.
- The ABC Workshop Fatality: A worker sustained fatal injuries while attempting to clear a jammed workpiece without shutting down the machine.
Evolution of Safety Measures
In response to these incidents, industries have made significant strides in enhancing safety measures. The introduction of safety guards, emergency stop buttons, and operator training programs has contributed to reducing the risk of accidents. However, the Russian lathe incident demonstrated that there is still room for improvement in ensuring the safety of workers in industrial settings.
What Are the Main Causes of Lathe Accidents?
Lathe accidents can result from a variety of factors, each contributing to the overall risk associated with operating these machines. Understanding these causes is crucial for preventing future incidents and improving safety practices.
Human Error
Human error is a leading cause of lathe accidents. This can include:
- Inadequate training or supervision
- Failure to follow safety protocols
- Distraction or fatigue while operating the machine
- Improper handling of tools and materials
Machine Malfunctions
Machine malfunctions can also contribute to accidents. Common issues include:
- Worn-out or damaged machine components
- Failure of safety mechanisms
- Inadequate maintenance and servicing
- Electrical or mechanical failures
The Impact on Industrial Safety Regulations
The Russian lathe incident has had a profound impact on industrial safety regulations, prompting changes that aim to enhance the protection of workers and prevent similar tragedies in the future.
Changes in Policy Post-Incident
Following the incident, regulatory bodies have introduced stricter guidelines for operating lathes and other heavy machinery. These changes include:
- Mandatory safety training and certification for operators
- Regular inspections and maintenance of machinery
- Improved safety guard designs and implementations
- Enhanced reporting and monitoring of safety incidents
Global Implications
The incident has resonated globally, leading to increased awareness and action across industries worldwide. International organizations have collaborated to establish unified safety standards and share best practices. This collective effort aims to create safer work environments and reduce the risk of accidents in industrial settings.
How Can Lathe Safety Be Improved?
Improving lathe safety requires a multifaceted approach, focusing on training, technology, and workplace culture. By addressing these areas, industries can significantly reduce the risk of accidents and enhance the safety of their operations.
Training and Education
Comprehensive training programs are essential for ensuring that operators are well-equipped to handle lathes safely. Effective training should cover:
- Proper machine operation and handling techniques
- Identification and mitigation of potential hazards
- Emergency procedures and response plans
- Ongoing education and skill development
Technological Advancements
Leveraging technology can also improve lathe safety. Innovations in this area include:
- Automated safety features and sensors
- Remote monitoring and control systems
- Advanced safety guard designs
- Integration of artificial intelligence and machine learning to predict and prevent malfunctions
The Role of Workplace Culture in Safety
Creating a strong safety culture is vital for ensuring the well-being of workers and preventing accidents. A positive workplace culture prioritizes safety and encourages employees to actively participate in maintaining a safe environment.
Encouraging a Safety-First Mindset
Promoting a safety-first mindset involves fostering an environment where:
- Employees feel empowered to report safety concerns without fear of reprisal
- Safety is integrated into daily operations and decision-making processes
- Regular safety meetings and discussions are held to address potential risks
- Continuous improvement in safety practices is encouraged and rewarded
Leadership and Accountability
Leadership plays a crucial role in shaping workplace culture. Effective leaders demonstrate a commitment to safety by:
- Leading by example and adhering to safety protocols
- Providing resources and support for safety initiatives
- Holding themselves and others accountable for maintaining safety standards
- Encouraging open communication and collaboration among team members
Lessons Learned from the Russian Lathe Incident
The Russian lathe incident has provided valuable lessons for industries worldwide, emphasizing the importance of safety and the need for continuous improvement in safety practices.
Key Takeaways for Industries
Some key takeaways from the incident include:
- The critical importance of adhering to safety protocols and guidelines
- The need for comprehensive training and education for operators
- The value of investing in advanced safety technologies and equipment
- The significance of fostering a strong safety culture in the workplace
Implementing Effective Safety Protocols
To prevent similar incidents, industries must implement effective safety protocols, including:
- Regular inspections and maintenance of machinery
- Clear communication of safety guidelines and procedures
- Encouraging employee involvement in safety initiatives
- Continuous evaluation and improvement of safety practices
The Importance of Regular Machine Maintenance
Regular machine maintenance is essential for ensuring the safe operation of lathes and preventing accidents. By implementing preventive maintenance measures, industries can significantly reduce the risk of machine malfunctions and improve overall safety.
Preventive Measures
Effective preventive maintenance measures include:
- Regular inspections of machinery components and systems
- Timely replacement of worn-out or damaged parts
- Lubrication and cleaning of machine components
- Calibration and adjustment of machine settings
Scheduling and Documentation
Proper scheduling and documentation of maintenance activities are crucial for ensuring that maintenance tasks are completed on time and effectively. This involves:
- Establishing a maintenance schedule and adhering to it
- Keeping detailed records of maintenance activities and findings
- Ensuring that maintenance personnel are trained and qualified
- Conducting regular audits to assess the effectiveness of maintenance practices
Employee Training and Safety Programs
Effective employee training and safety programs are vital for equipping workers with the knowledge and skills needed to operate lathes safely and prevent accidents.
Types of Training Programs
Training programs should cover a range of topics, including:
- Basic machine operation and handling techniques
- Safety protocols and emergency procedures
- Identification and mitigation of potential hazards
- Ongoing education and skill development
Measuring Effectiveness
To ensure the effectiveness of training programs, industries should regularly evaluate and update their programs based on feedback, incident reports, and industry best practices. This involves:
- Conducting assessments and evaluations of training outcomes
- Gathering feedback from trainees and instructors
- Updating training materials and methods as needed
- Incorporating new technologies and approaches to enhance learning experiences
The Psychological Impact on Workers
The psychological impact of workplace accidents, such as the Russian lathe incident, can be profound, affecting both the individuals involved and their coworkers. It is essential for industries to provide support and resources to help workers cope with the emotional aftermath of such incidents.
Coping Mechanisms
Workers affected by workplace accidents may benefit from various coping mechanisms, including:
- Counseling and psychological support services
- Peer support groups and networks
- Stress management and relaxation techniques
- Engagement in physical activities and hobbies
Support Systems in Place
Industries should establish support systems to assist workers in dealing with the psychological effects of workplace accidents. These may include:
- Access to professional counseling and mental health services
- Regular check-ins and follow-up support from management
- Opportunities for open communication and discussion of feelings
- Inclusion of mental health awareness in workplace safety programs
What Are the Legal Implications of Workplace Accidents?
Workplace accidents, such as the Russian lathe incident, can have significant legal implications for both employers and employees. Understanding these implications is crucial for ensuring compliance with regulations and protecting the rights of all parties involved.
Employer Responsibilities
Employers have a legal obligation to provide a safe working environment for their employees. This includes:
- Implementing and enforcing safety protocols and procedures
- Providing adequate training and supervision for workers
- Conducting regular inspections and maintenance of machinery
- Promptly addressing and rectifying identified hazards
Employee Rights
Employees have the right to a safe workplace and should be aware of their rights in the event of a workplace accident. These rights include:
- The right to report unsafe conditions without fear of retaliation
- The right to refuse work that poses an imminent danger to their safety
- The right to access information about workplace hazards and safety measures
- The right to seek compensation for injuries and damages resulting from workplace accidents
Case Studies of Improved Safety Practices
Several industries have successfully implemented improved safety practices in response to past incidents, serving as examples for others to follow in enhancing workplace safety.
Success Stories
Some notable success stories include:
- The XYZ Corporation: After a series of accidents, this company overhauled its safety protocols, resulting in a significant reduction in workplace incidents.
- The ABC Manufacturing Plant: Implemented advanced safety technologies and comprehensive training programs, leading to improved safety outcomes and employee satisfaction.
Lessons from Other Industries
Industries can learn valuable lessons from the experiences of others in improving safety practices. Key takeaways include:
- The importance of leadership commitment to safety
- The value of continuous improvement and innovation in safety measures
- The significance of employee involvement and engagement in safety initiatives
- The need for regular evaluation and adaptation of safety practices based on industry trends and developments
How Technology Can Enhance Lathe Safety?
Technology plays a vital role in enhancing lathe safety, providing innovative solutions to prevent accidents and protect workers. By leveraging technological advancements, industries can significantly improve the safety of their operations.
Innovations in Safety Equipment
Recent innovations in safety equipment for lathes include:
- Advanced safety guards and barriers to prevent operator contact with moving parts
- Sensors and alarms that detect potential hazards and alert operators
- Automated shut-off systems that halt machine operation in the event of a malfunction
- Wearable safety devices that monitor operator health and safety in real-time
The Future of Industrial Safety Technology
The future of industrial safety technology holds promise for further advancements in protecting workers and preventing accidents. Emerging trends and technologies include:
- Integration of artificial intelligence and machine learning to predict and prevent safety incidents
- Development of smart safety systems that adapt to changing conditions and environments
- Use of virtual and augmented reality for immersive safety training experiences
- Advancements in robotics and automation to reduce human involvement in hazardous tasks
FAQs About the Russian Lathe Incident and Workplace Safety
What led to the Russian lathe incident?
The Russian lathe incident was caused by a combination of factors, including inadequate safety measures, lack of proper training, and machine malfunction. These elements combined to create a hazardous situation that resulted in a tragic accident.
How can such incidents be prevented?
Preventing incidents like the Russian lathe incident requires a comprehensive approach that includes implementing stringent safety protocols, conducting regular training and education for operators, and investing in advanced safety technologies and equipment.
Are there specific safety standards for lathes?
Yes, there are specific safety standards for operating lathes, which are established by regulatory bodies and industry organizations. These standards outline the necessary safety measures and procedures to ensure the safe operation of lathe machines.
What are the common risks associated with lathe operations?
Common risks associated with lathe operations include entanglement with moving parts, contact with sharp tools, flying debris, and machine malfunctions. Proper safety protocols and training can help mitigate these risks.
How have industries responded to the incident?
In response to the Russian lathe incident, industries have implemented stricter safety measures, enhanced training programs, and invested in advanced safety technologies. These efforts aim to prevent similar incidents and improve overall workplace safety.
What resources are available for improving workplace safety?
Resources available for improving workplace safety include safety training programs, industry guidelines and standards, advanced safety equipment and technologies, and support from regulatory bodies and industry organizations. These resources can help industries enhance their safety practices and protect their workers.
Conclusion: Moving Forward with Safety in Mind
The Russian lathe incident serves as a stark reminder of the importance of safety in industrial settings. By learning from this tragedy and implementing effective safety measures, industries can significantly reduce the risk of accidents and protect their workers. Moving forward, a commitment to continuous improvement, innovation, and collaboration will be essential for creating safer work environments and ensuring the well-being of workers worldwide.
For further information on industrial safety standards and best practices, please visit the Occupational Safety and Health Administration (OSHA) website at www.osha.gov.

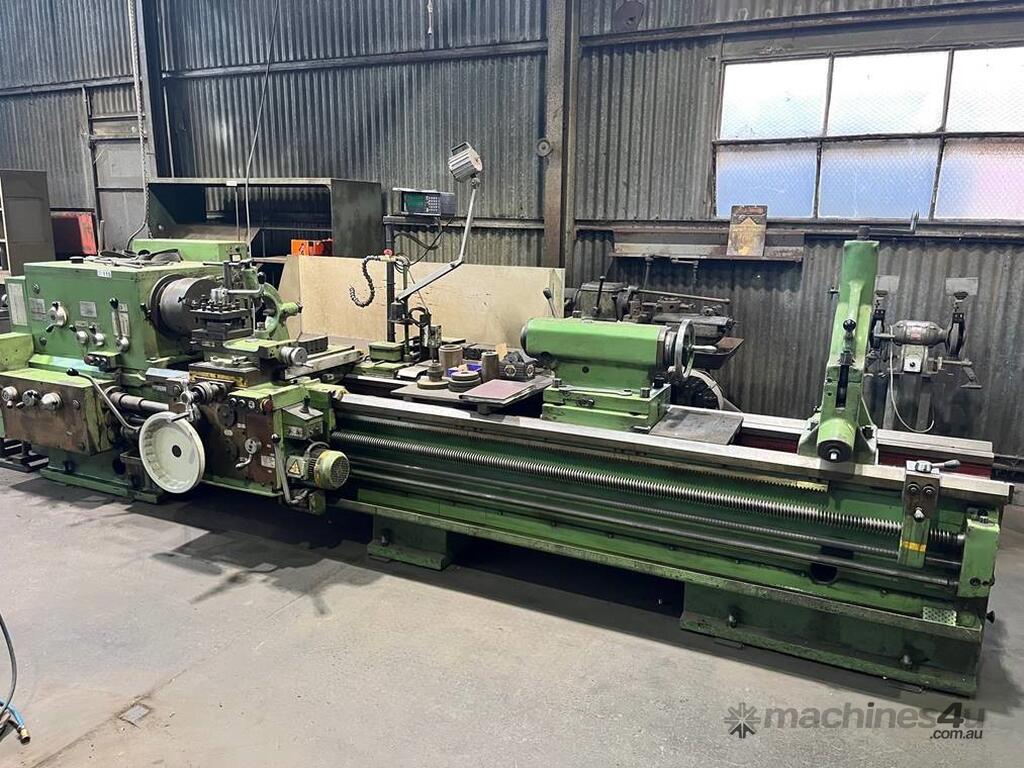