The term "Russian lathe accident" has become synonymous with one of the most tragic and widely discussed industrial mishaps in recent history. This incident, which took place in a Russian factory, serves as a stark reminder of the paramount importance of safety protocols in industrial settings. Despite advancements in technology and safety measures, accidents like these highlight the potential dangers that still exist in the workplace.
The Russian lathe accident involved a highly skilled worker who was tragically caught in a lathe machine due to a series of unfortunate events and lapses in safety measures. This incident not only resulted in a fatality but also prompted widespread discussions about workplace safety, equipment maintenance, and the enforcement of strict safety regulations. As such, it has become a case study for safety experts and industries worldwide, emphasizing the need for constant vigilance and adherence to safety standards.
Understanding the factors that led to the Russian lathe accident is crucial for preventing similar tragedies in the future. Through an in-depth analysis of the incident, including the operational environment, safety protocols in place, and the subsequent responses by authorities, we aim to provide valuable insights and lessons that can be applied across various industries. This article delves into these aspects, offering a comprehensive overview of the incident and highlighting the critical importance of workplace safety.
Read also:Insights Into Tammy Leppert A Mysterious Disappearance
Table of Contents
- Overview of the Incident
- The Importance of Safety Protocols
- How Can Industrial Accidents Be Prevented?
- Understanding Lathe Machines
- What Causes Lathe Accidents?
- Impact of the Russian Lathe Accident
- Case Study Analysis
- Global Reactions and Regulations
- How to Improve Workplace Safety?
- Lessons Learned from the Incident
- What Are the Future Trends in Industrial Safety?
- Role of Technology in Preventing Accidents
- Training and Education for Safety
- Frequently Asked Questions
- Conclusion
Overview of the Incident
The Russian lathe accident occurred in a bustling industrial area, where a skilled technician was performing routine operations on a lathe machine. Lathe machines, essential for shaping materials, are common in manufacturing industries. These machines, however, pose significant risks if not operated under strict safety guidelines. The incident unfolded when the worker's clothing got entangled in the rotating parts of the lathe, leading to a fatal outcome. This tragic event underscores the potential hazards posed by mechanical equipment and the dire need for stringent safety measures.
Initial investigations revealed that the accident was a result of multiple safety oversights. Despite the presence of safety protocols, lapses in their enforcement, coupled with inadequate training, contributed to the tragedy. The Russian lathe accident thus serves as a grim reminder of the inherent dangers in industrial environments, particularly when safety measures are neglected or improperly implemented.
Furthermore, this incident sparked a nationwide dialogue on workplace safety regulations and their enforcement. Authorities were compelled to revisit existing safety guidelines and implement more rigorous standards to prevent such accidents in the future. As industries across the globe watched the developments unfold, the Russian lathe accident became a pivotal moment in the discourse on occupational safety and health.
The Importance of Safety Protocols
Safety protocols are fundamental in preventing workplace accidents like the Russian lathe incident. These protocols encompass a wide range of measures, from proper equipment maintenance to comprehensive employee training. The primary objective of safety protocols is to minimize risks and ensure a secure working environment for all employees.
In the context of the Russian lathe accident, the lack of adherence to established safety protocols played a significant role in the tragedy. It highlighted the crucial need for regular safety audits and continuous monitoring of compliance with safety standards. Companies must prioritize safety by fostering a culture of vigilance and accountability among their workforce.
Moreover, safety protocols should be dynamic and adaptable to evolving industrial practices. As technology advances and new machinery is introduced, safety measures must be updated accordingly. This proactive approach can significantly reduce the likelihood of accidents and enhance overall workplace safety.
Read also:Movierulz Kannada A Deep Dive Into The World Of Kannada Cinema
How Can Industrial Accidents Be Prevented?
Preventing industrial accidents requires a multifaceted approach that addresses various aspects of workplace safety. The following strategies are essential for minimizing risks and promoting a safe working environment:
- Comprehensive Training: Employees should receive thorough training on operating machinery and understanding potential hazards. This training should be ongoing to keep workers informed of the latest safety practices.
- Regular Equipment Maintenance: Machinery should be routinely inspected and maintained to ensure it is in optimal working condition. Faulty equipment can lead to accidents, so timely repairs and replacements are crucial.
- Safety Audits: Conducting regular safety audits helps identify potential risks and areas for improvement. These audits should be carried out by qualified professionals who can provide actionable recommendations.
- Emergency Preparedness: Companies should have clear emergency protocols in place, including evacuation plans and first aid procedures. Employees should be familiar with these protocols to respond effectively in case of an incident.
- Cultivating a Safety Culture: Organizations should foster a culture of safety where employees feel responsible for their well-being and that of their colleagues. Encouraging open communication about safety concerns can lead to proactive problem-solving.
By implementing these strategies, industries can significantly reduce the risk of accidents and create a safer working environment for their employees.
Understanding Lathe Machines
Lathe machines are pivotal in various manufacturing processes, shaping materials into desired forms by rotating them against cutting tools. These machines are versatile and can work with a range of materials, including metal, wood, and plastic. Given their widespread use, understanding their operation and associated risks is crucial for ensuring workplace safety.
Lathe machines consist of several components, including the bed, headstock, tailstock, and carriage. The headstock holds the rotating spindle, while the tailstock supports the opposite end of the workpiece. The carriage moves along the bed, guiding the cutting tool to shape the material. Despite their utility, lathe machines can pose significant hazards if not operated correctly. The primary risks include entanglement, flying debris, and accidental contact with rotating parts.
To mitigate these risks, operators must adhere to strict safety guidelines. These include proper attire, such as fitted clothing and protective gear, to prevent entanglement. Additionally, operators should be trained to handle emergency situations and understand the machine's safety features, such as emergency stop buttons and guards.
What Causes Lathe Accidents?
Lathe accidents can result from various factors, often stemming from human error, mechanical failures, or inadequate safety measures. Understanding these causes is vital for preventing future incidents. Common causes of lathe accidents include:
- Operator Error: Inexperienced or improperly trained operators may make mistakes that lead to accidents. These errors can include incorrect setup, improper handling of tools, or failure to follow safety protocols.
- Mechanical Failures: Faulty or poorly maintained equipment can malfunction, posing significant risks to operators. Regular maintenance and timely repairs are essential to prevent such failures.
- Lack of Safety Measures: Insufficient safety protocols, such as missing guards or emergency stop buttons, can contribute to accidents. Companies must ensure that all necessary safety features are in place and functioning correctly.
- Distractions: Operators who are distracted or fatigued may be more prone to accidents. Maintaining focus and avoiding distractions is crucial for safe operation.
By addressing these causes, industries can enhance their safety measures and reduce the likelihood of lathe accidents.
Impact of the Russian Lathe Accident
The impact of the Russian lathe accident was profound, resonating across industries and prompting widespread discussions on workplace safety. The incident highlighted the severe consequences of neglecting safety protocols and underscored the need for stringent safety measures in industrial settings.
In the aftermath of the accident, there was a significant push for regulatory reforms and enhanced safety standards. Authorities introduced new regulations aimed at improving safety protocols and ensuring stricter compliance. Companies were urged to conduct thorough safety audits and implement comprehensive training programs for their employees.
Furthermore, the incident had a lasting impact on the affected community, with calls for greater transparency and accountability in workplace safety practices. It also served as a wake-up call for industries worldwide, emphasizing the importance of prioritizing employee safety and well-being.
Case Study Analysis
Analyzing the Russian lathe accident provides valuable insights into the factors that contributed to the tragedy and the measures that could have prevented it. This case study serves as a critical learning opportunity for industries seeking to enhance their safety protocols.
The analysis revealed several key areas for improvement, including:
- Safety Protocols: The lack of adherence to established safety protocols was a significant factor in the accident. Companies must ensure that safety measures are enforced consistently and that employees are well-trained in their implementation.
- Equipment Maintenance: Regular maintenance and inspections of machinery are essential to prevent mechanical failures. Companies should establish a maintenance schedule and address any equipment issues promptly.
- Training and Education: Comprehensive training programs are crucial for ensuring that employees are equipped with the knowledge and skills needed to operate machinery safely. Ongoing education helps keep workers informed of the latest safety practices.
By addressing these areas, industries can mitigate risks and prevent similar accidents from occurring in the future.
Global Reactions and Regulations
The Russian lathe accident prompted global reactions, with industries and regulatory bodies taking notice of the incident's implications. As a result, there was a renewed focus on enhancing workplace safety standards and ensuring strict compliance with safety regulations.
Regulatory bodies worldwide introduced new guidelines aimed at improving safety protocols and reducing the risk of industrial accidents. These measures included stricter enforcement of safety standards, increased inspections, and more rigorous penalties for non-compliance.
Furthermore, the incident sparked international discussions on best practices for workplace safety, with countries sharing insights and strategies to prevent similar tragedies. This collaborative approach has contributed to the development of more comprehensive safety regulations that prioritize employee well-being.
How to Improve Workplace Safety?
Improving workplace safety is a continuous process that requires commitment and collaboration from all stakeholders. The following strategies can help enhance safety measures and create a safer working environment:
- Leadership Commitment: Safety initiatives should be supported by leadership, with a clear commitment to prioritizing employee well-being. This commitment sets the tone for a safety-focused culture within the organization.
- Employee Involvement: Engaging employees in safety discussions and decision-making processes can lead to more effective safety measures. Employees should be encouraged to report safety concerns and contribute to problem-solving efforts.
- Continuous Improvement: Organizations should regularly review and update their safety protocols to ensure they remain effective and relevant. This includes staying informed of industry trends and incorporating new safety technologies.
- Safety Culture: Fostering a culture of safety involves creating an environment where safety is a shared responsibility. This includes promoting open communication, recognizing safe behaviors, and addressing safety concerns promptly.
By implementing these strategies, companies can create a safer workplace and reduce the likelihood of accidents.
Lessons Learned from the Incident
The Russian lathe accident offers several valuable lessons for industries seeking to enhance their safety protocols and prevent future tragedies. These lessons include:
- Importance of Safety Protocols: Adhering to established safety protocols is crucial for preventing accidents. Companies must ensure that these protocols are enforced consistently and that employees are trained in their implementation.
- Regular Maintenance: Proper maintenance and inspections of machinery are essential for preventing mechanical failures. Companies should establish a maintenance schedule and address any equipment issues promptly.
- Training and Education: Comprehensive training programs are crucial for ensuring that employees are equipped with the knowledge and skills needed to operate machinery safely. Ongoing education helps keep workers informed of the latest safety practices.
- Safety Culture: Fostering a culture of safety involves creating an environment where safety is a shared responsibility. This includes promoting open communication, recognizing safe behaviors, and addressing safety concerns promptly.
By learning from these lessons, industries can enhance their safety measures and create a safer working environment for their employees.
What Are the Future Trends in Industrial Safety?
As industries continue to evolve, new trends in industrial safety are emerging, driven by technological advancements and changing workplace dynamics. The following trends are shaping the future of industrial safety:
- Automation: The integration of automation and robotics in industrial processes can reduce the risk of accidents by minimizing human intervention in hazardous tasks. Automation can also enhance efficiency and productivity.
- Wearable Technology: Wearable devices equipped with sensors can monitor workers' health and safety in real-time. These devices can alert workers to potential hazards and provide valuable data for improving safety protocols.
- Virtual Reality Training: Virtual reality (VR) technology is being used to simulate hazardous scenarios, allowing workers to practice safety procedures in a controlled environment. VR training can enhance learning outcomes and improve safety awareness.
- Data Analytics: Data analytics can provide insights into safety trends and identify areas for improvement. Companies can use data to make informed decisions and implement targeted safety initiatives.
By embracing these trends, industries can enhance their safety measures and create a safer working environment for their employees.
Role of Technology in Preventing Accidents
Technology plays a crucial role in preventing industrial accidents by enhancing safety measures and improving workplace conditions. The following technological advancements are contributing to safer industrial environments:
- Automation and Robotics: Automating hazardous tasks can reduce the risk of accidents by minimizing human intervention. Robotics can perform repetitive tasks with precision, reducing the likelihood of human error.
- Internet of Things (IoT): IoT devices can monitor equipment and environmental conditions in real-time, providing valuable data for preventing accidents. These devices can alert operators to potential hazards and allow for proactive maintenance.
- Artificial Intelligence (AI): AI algorithms can analyze safety data and identify patterns that may indicate potential risks. Companies can use AI to implement predictive maintenance and enhance safety protocols.
- Augmented Reality (AR): AR technology can provide workers with real-time safety information, such as equipment status and safety instructions. This technology can enhance situational awareness and improve decision-making.
By leveraging these technologies, industries can enhance their safety measures and create a safer working environment for their employees.
Training and Education for Safety
Training and education are fundamental components of workplace safety, equipping employees with the knowledge and skills needed to operate machinery safely and respond to emergencies. The following strategies can enhance training and education efforts:
- Comprehensive Training Programs: Companies should develop comprehensive training programs that cover all aspects of workplace safety, including machinery operation, emergency procedures, and safety protocols.
- Ongoing Education: Ongoing education helps keep employees informed of the latest safety practices and industry trends. Companies should provide opportunities for continuous learning and development.
- Hands-On Training: Hands-on training provides employees with practical experience and enhances learning outcomes. Companies should incorporate hands-on training into their safety programs.
- Use of Technology: Technology, such as virtual reality and simulation, can enhance training efforts by providing realistic scenarios for practice. Companies should leverage technology to improve training outcomes.
By prioritizing training and education, industries can enhance their safety measures and create a safer working environment for their employees.
Frequently Asked Questions
1. What led to the Russian lathe accident?
The Russian lathe accident was primarily caused by a combination of operator error, mechanical failure, and inadequate safety measures. The worker's clothing became entangled in the lathe machine, which resulted in a fatal outcome.
2. How can industries prevent similar accidents?
Industries can prevent similar accidents by implementing comprehensive safety protocols, providing regular training and education, conducting routine equipment maintenance, and fostering a culture of safety within the organization.
3. What are the key lessons learned from the Russian lathe accident?
The key lessons learned from the Russian lathe accident include the importance of adhering to safety protocols, the need for regular equipment maintenance, the value of comprehensive training programs, and the significance of fostering a safety culture.
4. How is technology contributing to industrial safety?
Technology is contributing to industrial safety by enhancing safety measures and improving workplace conditions. Advancements in automation, IoT, AI, and AR are helping to reduce the risk of accidents and create safer industrial environments.
5. What role does training and education play in workplace safety?
Training and education play a crucial role in workplace safety by equipping employees with the knowledge and skills needed to operate machinery safely and respond to emergencies. Comprehensive training programs and ongoing education are essential for ensuring workplace safety.
6. What are the future trends in industrial safety?
Future trends in industrial safety include the integration of automation and robotics, the use of wearable technology, virtual reality training, and data analytics. These trends are shaping the future of industrial safety and contributing to safer working environments.
Conclusion
The Russian lathe accident serves as a poignant reminder of the importance of workplace safety and the need for stringent safety measures in industrial settings. By understanding the factors that contributed to the incident and learning from the lessons it offers, industries can enhance their safety protocols and prevent similar tragedies in the future. Embracing technological advancements and fostering a culture of safety will be key to creating safer working environments and protecting the well-being of employees.

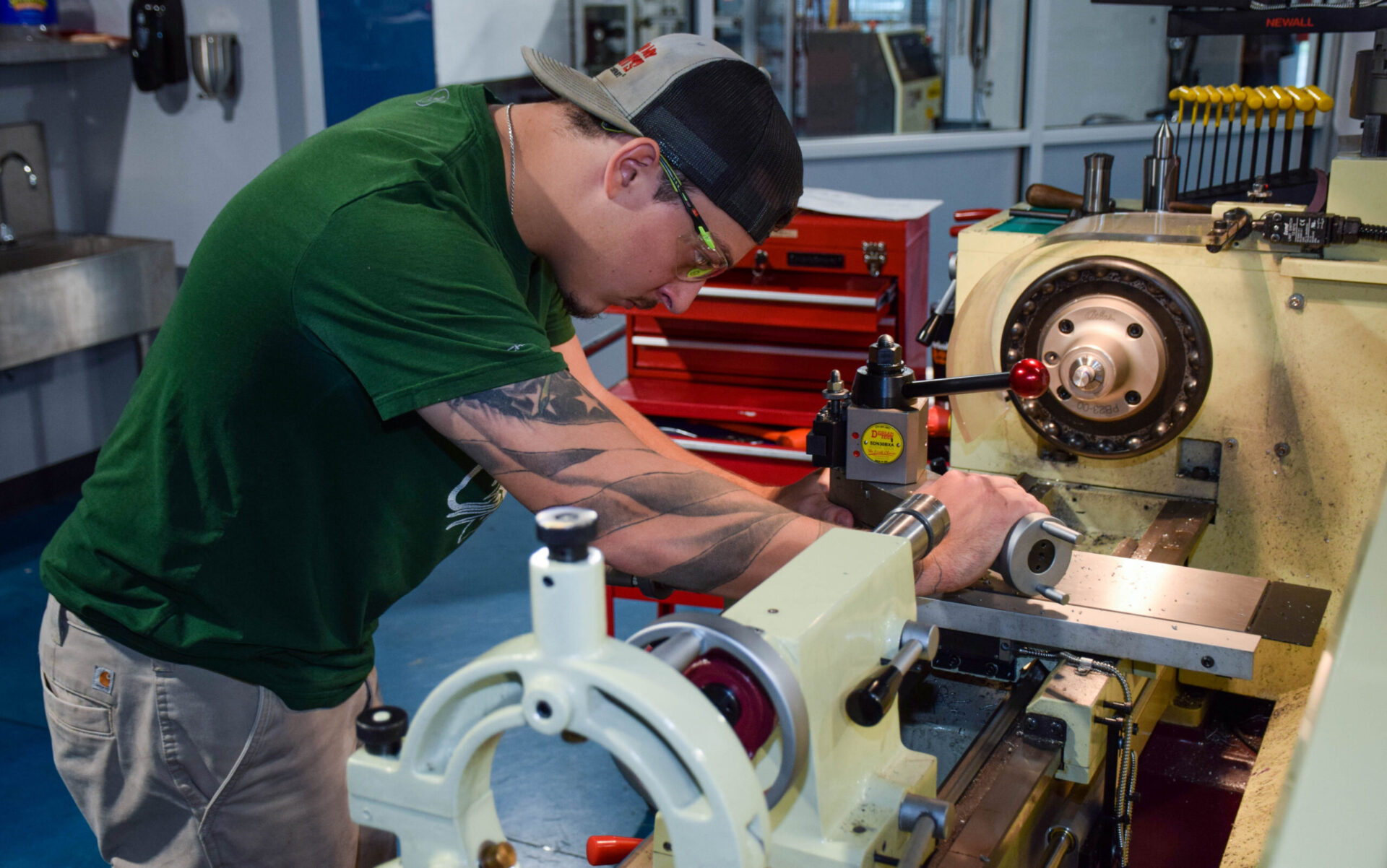